.png?width=2000&height=1000&name=Cool%20Sorption%20VRU%20Technology%20(4).png)
A standard Cool Sorption Vapour Recovery Unit (VRU) is based on the Carbon Vacuum Adsoprtion (CVA) process. However, for some customers this technology is not advantageous because of size, special design conditions, lack of absorbent etc. For such situations, Cool Sorption also offers a range of simple variations to the CVA process as well as alternative, custom-made designs.
CVA (Carbon Vacuum Adsorption) – 2 activated carbon beds
The by far most commonly used VRU technology is based on adsorption on activated carbon followed by regeneration under vacuum. In Cool Sorption terminology we call it the CVA (Carbon Vacuum Adsoprtion) process. This process utilises two or more fixed beds filled with activated carbon (AC), a vacuum pump and an absorber column
.png?width=600&height=389&name=Copy%20of%20Untitled%20Design%20(768%20x%20497%20px).png)
- The inlet gasses to the VRU (typically containing 20-50 vol% hydrocarbons) are led to the AC beds. Due to the microporous structure and high surface area of activated carbon, the hydrocarbon gasses are adsorbed in a thin layer on the surface of the activated carbon, resulting in a very low concentration (10 g/Nm3 to 150 mg/Nm3) of hydrocarbons in the vapours exiting the AC beds. At any time, one of the beds is in “desorption” mode (i.e. regenerating by removing the adsorbed hydrocarbon gasses), while the other is in “adsorption” mode (i.e. receiving and adsorbing the incoming hydrocarbon gasses).
- Before the capacity of a carbon bed in adsorption mode is reached (i.e. before a breakthrough can occur), the bed shifts to regeneration mode. The operation of the beds is switched in this way every 15 minutes. When in regenerative mode, the hydrocarbon gasses are desorbed from the activated carbon using a vacuum pump.
- Regeneration of the AC beds takes place in three stages. In the first stage, the bed is evacuated of remaining inlet vapours left in the void spaces of the carbon bed vessel. In the second stage, the pressure in the bed continues to fall until it reaches a level at which the hydrocarbons begin to desorb from the surface of the activated carbon. The bulk of the hydrocarbons are removed during this stage. During the third stage, a small bleed of (ambient) purge air is introduced into the AC bed to assist the removal of the remainder of the hydrocarbons from the activated carbon and thus complete the regeneration process.
- The gas recovered with the vacuum pump will have a very high concentration of the VOC gasses (approx. 95 vol% VOC in 5 vol% air). This gas is led to an absorber column, where most of the hydrocarbons are absorbed in a counter-current flow of an appropriate absorbent.
- The gas exiting the absorber column will be saturated with hydrocarbon gasses from the absorbent and is recycled by mixing it with the inlet gasses to the VRU, going to the activated carbon beds.
As mentioned above, the AC beds are regenerated by means of vacuum; the vacuum pump system is therefore a vital component of the VRU. During the regeneration phase, the level of vacuum drawn in the AC beds is between 100 and 50 mbara.
Based on many years of experience with CVA systems, Cool Sorption launched a series of pre-engineered, standardised VRUs – especially for truck and railway terminals – in 2013. These VRUs (named Depot Series™ or DS-Series™) are mainly for terminals with low to medium throughput and have proven extremely reliable and successful.
CVA (Carbon Vacuum Adsorption) – 3 activated carbon beds
In 2012, Cool Sorption developed a proprietary CVA concept with not two, but three activated carbon beds. The operation of the system is similar to the system described above with two carbon beds with a few exceptions. At all times during operation, two of the AC bed are in "adsorption mode" while the last AC bed undergoes regeneration by means of vacuum.

This unique configuration offers the following distinct advantages compared to the traditional 2-bed VRU:
- Reduced pressure drop through the carbon beds, thereby providing a lower overall pressure drop through the three-bed VRU compared to a conventional 2-bed configuration for the same vapour capacity.
- Smaller Carbon Bed vessels required, thereby reducing the unit fabrication price and allowing for easier transport, handling and installation of the vessels as well as a smaller footprint of the VRU
- Reduced overall activated carbon volume required, thereby decreasing consumption of carbon.
- Smaller diameter inlet and vent vapour piping required, thereby decreasing piping and component costs and allowing for easier handling of these components.
- First stage of carbon bed depressurisation at the start of regeneration is performed by internal equalisation with the other newly regenerated carbon bed still under vacuum. As a result, the volume of air entering the system during equalisation and purge phases is minimised, allowing for more efficient vacuum pump utilization and reduction of power requirements.
- Reduced internal recycle of hydrocarbons
- Reduced overall power consumption
The vacuum skid and the absorber column will remain the same as for a VRU with the previously described 2 beds configuration.
Based on this 3-bed system, Cool Sorption has developed a series of pre-engineered 3-bed systems, marketed as the Terminal Series™ – typically installed in marine terminals and other terminals with high/very high loading rates
ACVA (pre-Absorption/Carbon Vacuum Adsorption) – with 2 or 3 activated carbon beds
The ACVA process is a modification of the CVA process. It is advantageous for special cases where the hydrocarbon concentration in the inlet vapours is very high, if a lean absorbent (with extra good absorption properties) is available and/or if the inlet vapours contain compounds that might be harmful to the activated carbon.
In this process, a pre-absorber (sometimes with cooling of absorbent and/or overpressure in the column) is used to pre-treat the client’s vapour feed prior to entering the CVA unit. This may enables a much smaller VRU and/or increases the stability of the process and the lifetime of the activated carbon.
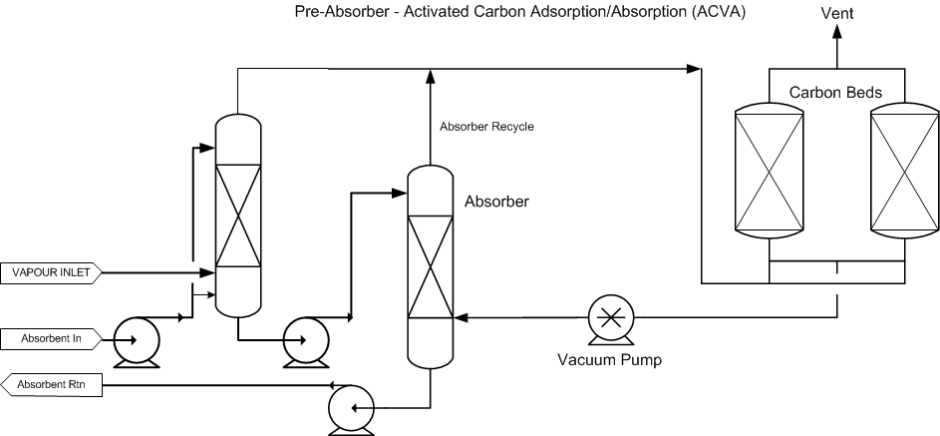
The raw vapours from loading are treated in the upper packing section of the column, while the hydrocarbons stripped out from the activated carbon beds by the vacuum pump pass through both the bottom and the top packing sections.
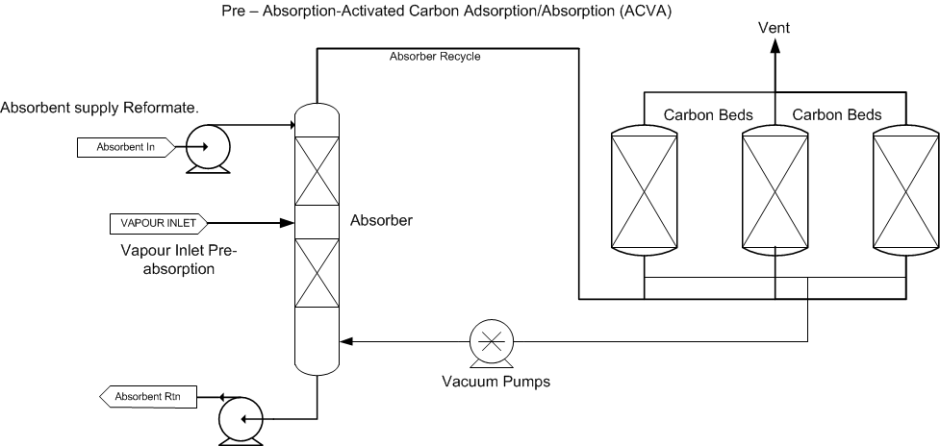
CVPC (Activated Carbon Adsorption/Pressurized Condensation) – with 2 or 3 activated carbon beds
In cases where the customer has no possibility to use an absorbent for the VRU, a CVPC technology can be used.
The concept can be used for both 2 and 3 bed systems, and the absorber is replaced by a compressor, a condenser and a collection tank for the recovered product. This recovered product consists of the components which evaporated in the first place and is therefore very light. It needs to be kept under pressure and can be returned in a relatively small line to a refinery facility for further treatment.
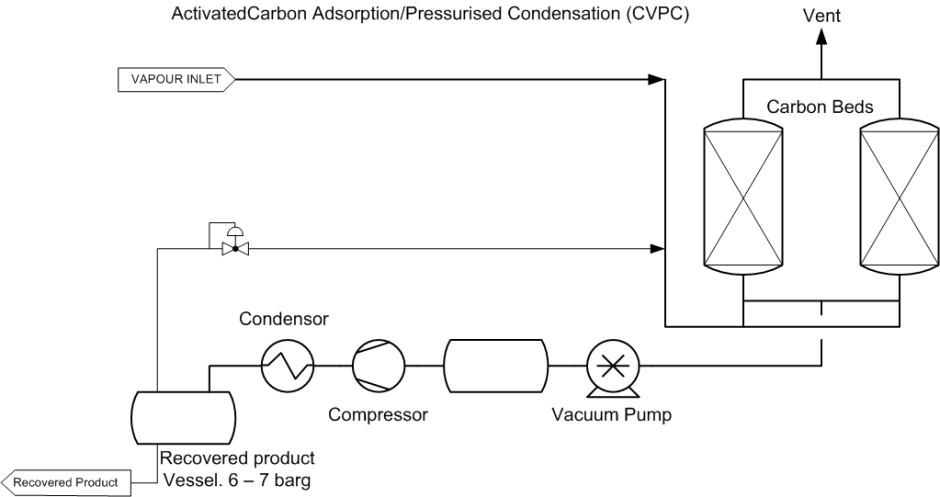
PLA (Pressurized Liquid Absorption)
In some applications, an acceptable recovery can be achieved using the very simple PLA process, as shown in the sketch below:
A lean (and/or chilled in order to reduce the vapour pressure at the operative conditions) absorbent will be recirculated over an absorber column. The incoming vapour stream to the VRU is first pressurized using a compressor and then passed counter current through the absorber column at the high pressure conditions. The combination of pressure and/or cooling and/or a lean absorbent can greatly improve the absorption.
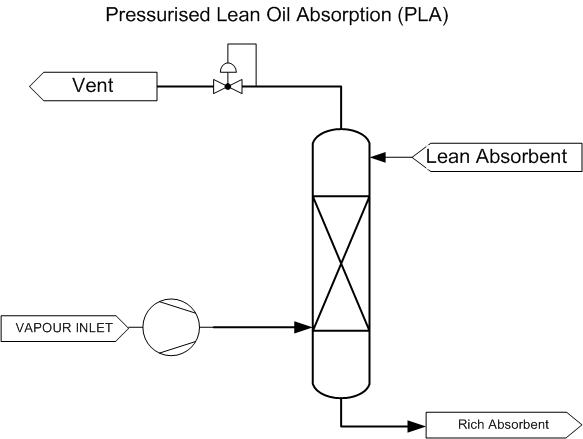
Applications are characterized by one or more of the below factors:
- Less stringent emission requirements
- Extreme limitations in VRU footprint
- Availability of an absorbent with low vapour pressure (< 30 kPa)
Cool Sorption has built a number of these systems for on-board VRUs for crude oil recovery. They are not suitable for all crude oil compositions and the efficiency is not very high (>70% recovery) but the systems have proven extremely reliable (more than 99,5% availability).
CLA (Cold Liquid Absorption)
Cold Liquid Absorption - CLA - was patented in 1983 as Cool Sorption’s “original” process for vapour recovery. More than 75 of these units were delivered and a large number are still in operation. Although not widely used today, this technology remains an interesting option in some applications.
When a hydrocarbon-rich vapour is brought into contact with a hydrocarbon liquid, equilibrium between the liquid and vapour phases is reached, depending on the partial pressures of the combined hydrocarbon-rich media. This principle forms the basis of the cold liquid absorption process.
The hydrocarbon-rich vapour stream is passed through an absorber column counter-current to a flow of a cold, high molecular weight hydrocarbon liquid (e.g. kerosene). Since the liquid has a much lower partial pressure than the vapour and the liquid is present in greater quantity, the resulting equilibrium partial pressure is much lower than that of the inlet vapours alone. Consequently, most of the hydrocarbon vapours can no longer be supported in the vapour phase and are absorbed into the liquid phase.
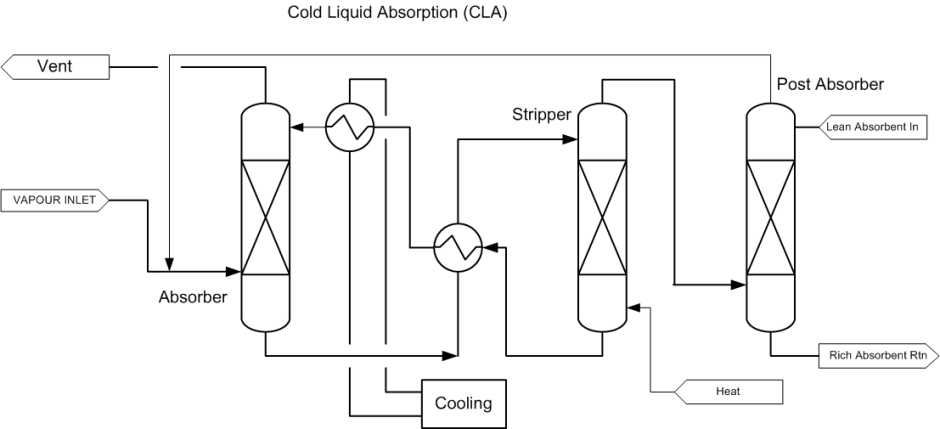
Ready to talk?
Let us know how we can help you!